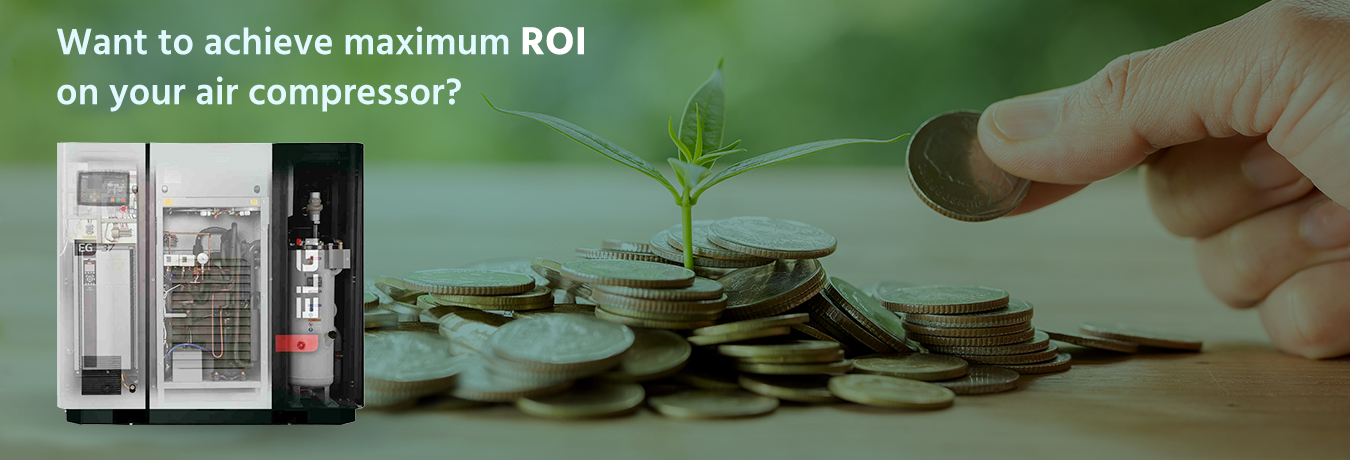
Achieve Maximum Roi With Your Air Compressor
Air compressors play a vital role in the majority of industries where compressed air is crucial for manufacturing processes. The main challenge here is achieving optimal efficiency with energy and cost savings. Are you worried about how to achieve a return on investment in a lesser period? Then, here are a few things that are important for you to consider and to know where to look for savings.
Step 1: Size Up Your Needs
When it comes to choosing the size of your air compressor, bigger is not always better. An energy-efficient air compressor is what you need to suit your requirements regardless of the size. A compressor will load continuously when its production capacity matches the air requirement. It costs more energy when a compressor is running in an unloaded condition. So, never buy an oversized air compressor. Demand a sizing audit from the manufacturers to pick the perfect-sized air compressor.
Step 2: Match Your Frequency
For industries with stable air demand, the right-sized compressors are sufficient. But what about industries that have varying demand patterns and for industries trying to increase their manufacturing capacity? The Variable Frequency Drives (VFDs) can satisfy these requirements. The VFD technology has been used for many years in air compressors. The Variable Frequency Drives works by reducing the motor speed to match the actual air demand by lowering the flow thus resulting in low power consumption. A sizing audit is a must to evaluate the need for a VFD.
Advantages of installing a VFD.
- Increased energy efficiency,
- Reduced downtime of the system,
- Improves the working capacity of the components,
- Helps in optimal performance,
- Reduced starting currents.
Step 3: Ensure a Smooth Flow
It is important to ensure a smooth flow for increased efficiency. It is better to have a shorter distance between the air compressor and the application. Also, minimize the bends that route to the application to ensure efficiency. Aluminum, steel, and plastic piping are the commonly used piping systems in India. Steel piping is cheaper when compared to aluminum piping but the risk of corrosion is more. Industrial Air Solutions offer innovatively designed aluminum piping systems that reduce installation cost with uncompromising quality. The fittings and material offer a flexible system for long-term operation. It is highly necessary to check for leaks in the system as it leads to higher energy consumption and air wastage.
Step 4: Air Audits
Air audits can help you evaluate the efficiency of your compressed air system. They help you in identifying damage and preventing leaks to optimize the usage. Compressor manufacturers conduct air audits to understand the varying air demands and thus saving energy and costs. Apart from this an air audit also helps in realizing the unwanted usage of the air compressor.
Step 5: Regular Check-up
Regular monitoring of the compressed air system is highly essential. To maintain the chosen pressure, the air compressors cycle on and off regularly. The below-given points can help you save maximum on your chosen air compressor. Periodically review the air usage and identify the areas of improvement for maximum savings.
- Turn off the air compressor when there is no need for compressed air,
- Maintain the air pressure only as required,
- Change the air filters regularly,
- Check for air leaks,
- Review the piping infrastructure.
Step 6: Determine the Life Cycle Cost
It is very important to know the life cycle cost of your air compressor to attain maximum returns. This analysis helps in examining everything right from the raw material selection to the final waste removal. The life cycle cost analysis also includes the operating costs and the maintenance cost. Proper usage and maintenance of the air compressor can help you save a lot of energy and money. The LLC calculation usually varies from industry to industry. The 3 major factors that are considered here are as follow.
- Capital Equipment Expenditure (Capex)
- Ordinary Maintenance Costs
- Energetic Consumption Costs