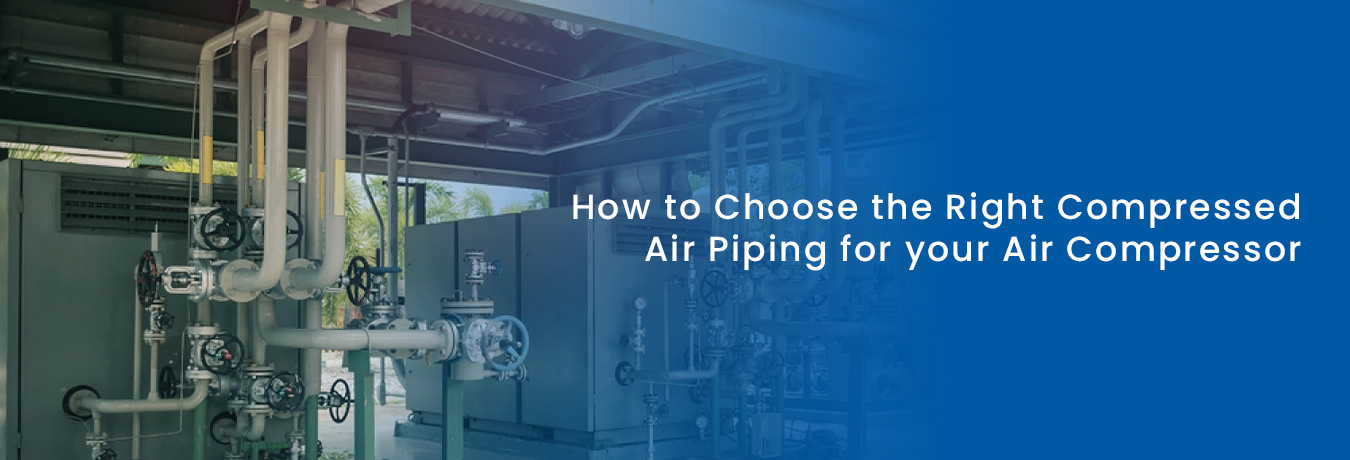
How to choose the right compressed air piping for your air compressor
Compressed air is an essential component of many industrial and manufacturing processes, and ensuring that your compressed air system is reliable, efficient, and safe is crucial. One important aspect of compressed air systems is the piping used to transport the compressed air throughout your facility. In this blog, we will discuss the key considerations when designing and installing compressed air piping.
Material selection: The choice of material for compressed air piping is critical to ensure system performance and safety. The most common materials used for compressed air piping are black iron, copper, aluminum, and plastic. Black iron is commonly used for larger, high-pressure systems, but it can corrode over time. Copper is a durable material that is resistant to corrosion and can handle high pressures, but it can be costly. Aluminum is lightweight and corrosion-resistant, but it is not suitable for high-pressure systems. Plastic piping is easy to install and inexpensive, but it may not be suitable for all applications.
Sizing: Choosing the right size of compressed air piping is critical for ensuring adequate airflow and system efficiency. Undersized pipes can cause pressure drops, reducing the effectiveness of your compressed air system. Oversized pipes can result in higher installation costs and increased energy consumption. The size of the piping should be determined based on the required flow rate, system pressure, and the length of the piping run.
Layout: The layout of compressed air piping should be designed to minimize pressure drops and ensure efficient flow. Straight runs of piping with minimal bends and fittings are preferred. Avoid sharp turns and elbows that can cause turbulence and reduce airflow. Piping should be installed with a slight slope to allow condensate to drain from the system.
Installation: Proper installation is critical to ensure the safe and efficient operation of compressed air piping. Pipes should be securely anchored to prevent movement and vibration, which can cause leaks and reduce system efficiency. All connections should be properly tightened and sealed with appropriate fittings and gaskets. Properly installed shut-off valves and pressure relief valves should be installed as necessary.
Maintenance: Regular maintenance is essential for the safe and efficient operation of compressed air piping. Regular inspections should be performed to check for leaks, corrosion, and damage. Condensate should be drained from the system regularly, and filters should be replaced as necessary. Any repairs or modifications to the system should be made promptly by trained personnel.
In conclusion, compressed air piping is a critical component of many industrial processes. Choosing the right material, sizing, layout, installation, and maintenance are key considerations to ensure the safe and efficient operation of your compressed air system. Properly designed and installed compressed air piping can improve system efficiency, reduce energy costs, and increase productivity.